Strategies to improve on-time performance
Is your lead time inflated by fear? Nearly every supply chain leader answers yes to that question: their lead times are inflated due to excessive conservatism of missing on-time performance. They have rightly justified the need to pad out lead times to avoid the risk of not meeting delivery schedules. As a result, many errors can arise in the supply chain, such as:
- Vendor delays because of quality issues, product rejections, etc.
- Shipment delays due to inaccurate documentation, late container bookings, or port congestion
- Delivery delays due to picking errors, late scheduling, or late pickup
- Poor supply chain management, including inaccurate forecasts, incorrect safety stock levels and late purchase ordering
Purchasing, logistics and customer service teams often inflate lead times to ensure shipments meet delivery times, even if excessively early. Based on such inaccuracies, sales teams may overpromise to customers which could result in skewed customer expectations. In either circumstance of running ahead of or behind schedule, the result is a mismanaged supply chain with insufficient control.
The cost of missing on-time deliveries
A business’s cost in operating an inefficient supply chain with extensive lead times to achieve on-time delivery can be measured by their inventory carrying cost; a metric that compares business expenses related to holding and storing unsold goods to the value of inventory on hand. The greater the lead time inflation, the more inventory on hand. The following table shows how these costs often break down.
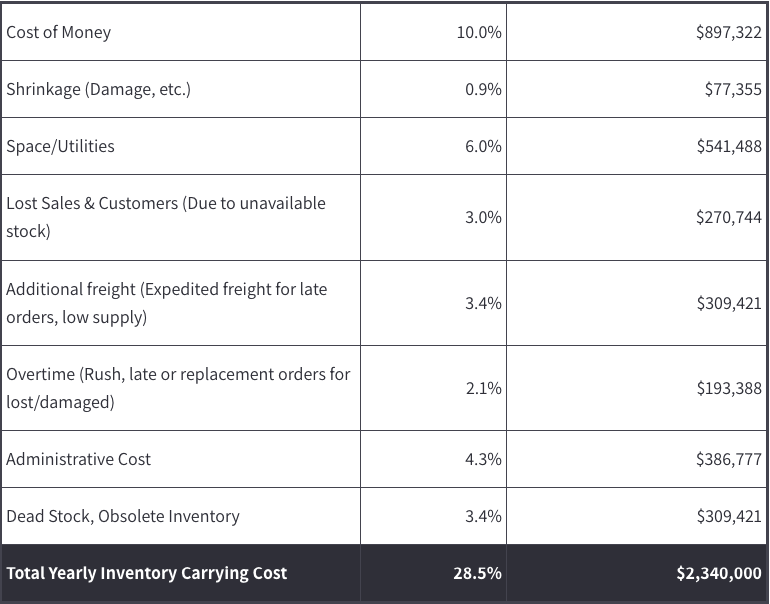
A company creating gradual steps to improve on-time performance would reduce or remove additional freight costs (3.7%), overtime costs (2.3%), and lost sales and customers (3.2%). This equates to nearly 10% of costs caused by poor on-time delivery performance.
Unfortunately, this is easier said than done. Supply chain leaders and their teams often justify their inflated lead times to achieve their KPI targets. However, the key to reducing costs is tightening lead times so that the supply chain runs on time, rather than behind or well ahead of time. Inflated lead times are a symptom, not the cause. Often the catalyst for improving lead times and cutting costs comes when a business needs to rapidly improve financial performance, for instance, when a new CEO is hired.
The impact of on-time performance on revenue
In 2017, Walmart introduced penalties for suppliers who failed to deliver as expected – and other large retailers have since followed suit. They use the on-time in-full (OTIF) metric to measure compliance. Walmart’s OTIF compliance guidelines require the shipment to be delivered within a specific window (early arrival is not counted as on-time), packaged and labelled as directed, and the product to arrive as ordered.
This has increased performance expectations for some companies to improve on-time last-mile delivery. Heinz sees the upside in this, using the structure of OTIF penalties as a spur to embed OTIF principles internally. Given how on-time performance improves overall efficiency, reduces costs, increases customer satisfaction, and increases revenue - there are substantial rewards for a company and their suppliers, to commit to improving on-time delivery.
How to achieve industry-leading on-time performance levels?
Working towards a 100% on-time delivery performance requires organizational focus to maintain smoothly running operations. Here are a few steps you can implement either with your team or with the help of supply chain experts. Before on-time performance can be improved, the root cause of deviations from planned lead times must be identified. Begin by creating a baseline:
Create a holistic understanding of your supply chain. Before on-time performance can be improved, the root cause of deviations from planned lead times must be identified. Begin by creating a baseline:
- Review customer service performance requirements and expectations.
- Document each process step in your supply chain, including purchasing (ordering and production), shipping execution (pickup, consolidation, main haul, port clearance, on-carriage and delivery to the warehouse), warehouse operations (processing and fulfillment), and final-mile delivery.
- Document contractual service level agreements, including all vendors and the logistics providers involved with inbound or outbound transport or warehousing, and compare them to actual performance.
Measure and implement improvement initiatives. Once a baseline is determined, the analysis phase can begin by measuring the actual lead times of each process step and comparing them to the agreed service level agreements and customers’ service performance requirements and expectations. The outcome will be a list of opportunities for improving processes and reducing costs. Map your improvement initiatives on a 2x2 chart and start with the measure that is easiest to implement and delivers the highest yield. Once prioritized, this will be the roadmap for improvement. Some process improvements may be simple to implement, such as using better ocean routing options, but others might take more time, such as changing the distribution center of gravity to be closer to the core customer base. The last step is to implement the improvement measures.
Leverage supply chain visibility. Many on-time performance improvements are only possible if there is good visibility across the supply chain. McKinsey describes better visibility as a “real-time performance cockpit covering all critical supply-chain performance metrics across its planning, manufacturing, and logistics execution processes.” In effect, it is leveraging the data and information already collected to create a digital platform that integrates both internal and external supplier systems.
With improved visibility, all stakeholders in the supply chain can accurately predict inventory, manage purchase orders, and follow shipments. By using validated data, supply chain teams have an opportunity to achieve industry-leading on-time performance levels.
Conclusion
Supply chain leaders everywhere feel the pain of poor on-time delivery performance, often in their bottom line. Poor management of this critical process results in an incredible number of delays, loss of revenue and unsatisfied customers. By implementing the proven initiatives above, your supply chain can realize success through creating a holistic plan forward, measuring and carrying out improvement initiatives, and increasing your supply chain’s visibility. Don’t let yourself fall victim to the cycle so many supply chain leaders get stuck in. Take the steps necessary to get ahead of your delivery performance issues and gain the upper hand over your competitors in the process.