How to improve your landed costs
What is landed cost?
Landed cost is the sum of all costs involved with getting a product from origin to its destination.
Unfortunately, that isn’t necessarily as clear-cut as it sounds.
At its narrowest, a landed cost definition only includes dock to dock costs, that is, those costs associated with the shipment of a product from the supplier’s dock to the shipper’s dock. Often the purchase price is included as well. This broader definition is especially useful for supply chain managers comparing the cost to source a product from different locations. Some other definitions include indirect costs like overheads as well.
The definition we consider the most optimal and used in this article includes all major cost items and is often referred to as “total landed cost”, i.e. the total cost of a product up until it reaches the buyer’s doorstep.
Understand the basics:
How is landed cost calculated?
A comprehensive formula for calculating landed cost considering all major cost items is:
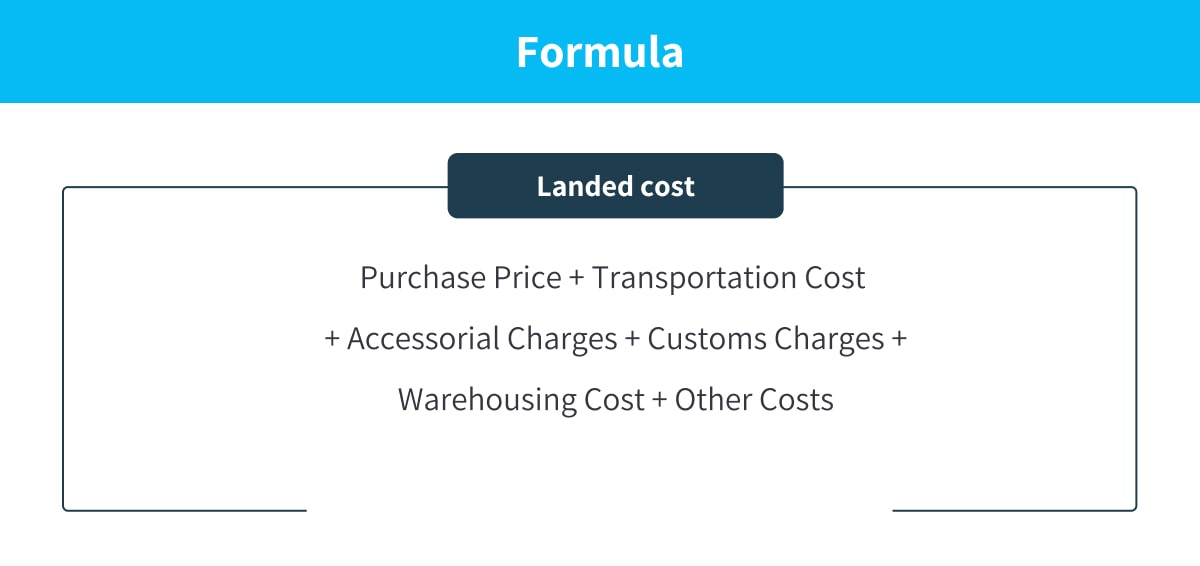
Purchase price
The cost of purchasing the products or raw material for producing the products to sell.
Transportation cost
The cost of shipping the goods, including pickup, main freight and delivery to the warehouse (or cross-docking) and delivery costs to the customer. The transportation costs are determined by several variables, such as how far the shipment needs to go, which types of transportation are used, shipment density or volume, etc.
Accessorial charges
Additional freight-related charges not included in the freight cost but incurred during shipment. The largest of these are often detention and demurrage costs.
Customs charges
Fees like duty, tariffs, import licenses and value-added tax (VAT). Customs agencies may also apply fines.
Warehousing cost
The direct (shelf space, shelf time) cost and potentially also indirect costs of storing goods at the shipper’s or their logistics provider’s warehouse.
Other costs
There are various other charges which are either usually minor (e.g. currency fluctuations, occasional supplier quality inspections), first-time only (e.g. legal fees for establishing supplier agreements, factory audits) or relevant in only a few circumstances (e.g. letter of credit payment, product liability insurance).
Common pitfalls when calculating landed cost
For some companies, their primary method for managing landed cost is to get the cheapest container cost, but this is a dangerous path. The $500 they save on a container might easily be wiped out with other costs that make up landed cost.
Most supply chain managers work to landed cost and measure based on the information they readily have. Unfortunately, key data in operating systems is often wrong, aged or just missing, meaning landed cost is often not properly calculated. Mistakes commonly occur in the following ways:
Averaging container costs
Many companies go wrong by averaging e.g. container shipping costs. That can be very misleading when there are multiple SKUs with different dimensions and weights in a container.
Unknown accessorial charges
By their very nature, these costs aren’t always known in advance and can be difficult to estimate. They do eventually come in on the invoice but are often aggregated in the accounting function and are therefore either averaged or even left out altogether from a landed cost calculation.
Aged data
Landed cost calculations are often not up to date. That's because most supply chain managers don’t have the time each month to run extracts from various systems and manually recalculate landed cost.
All these issues can have an adverse effect on your landed cost.
Here’s a real example. The purchasing department of one large customer, who shipped well over 10,000 containers a year, had struck a great full container load purchasing price for a particular product. The company took advantage of this great price. So much so, their warehouse capacity couldn’t accommodate the large quantities coming in. Containers were backing up at the warehouses and at port. They soon knew they had a problem but for some time didn’t really understand the magnitude. The detention and demurrage charges were aggregated in the accounting system and therefore could not link back to a specific SKU to adjust the assumed landed cost. Without that feedback loop, their purchasing behavior continued unchecked and the problem continued for several more months than it should. Their good deal became a hard loss.
Solutions to calculating landed cost
Building a robust and accurate landed cost calculation tool using internal company resources may sound intimidating, involving a lot of effort and overwhelming detail, but it is completely achievable. The following steps provide an outline of how this should be approached:
- Define how landed cost will be measured. The formula recommended in this article includes those groupings of cost that make the biggest difference.
- Establish a framework for calculating landed cost. This can be done by using spreadsheets or internally developed tools.
- Identify the best source for each cost element. Unfortunately, cost elements are rarely stored in just one system, so this detective work will likely be a very time-consuming manual task.
- Product extracts from the identified sources and build queries and business rules (e.g. to separate and apportion invoice costs) to reorganize costs by SKU.
- Set up an efficient process for regularly extracting the required data and rerunning the calculations.
Pro-Tip:
Don’t stand on the sidelines waiting to accumulate sufficient data. Start straight away with data at hand and begin developing the equation adding metrics such as payment terms, transit time and manufacturing lead time. This “quick off the block” approach builds momentum and soon identifies which cost elements are missing.
However, most supply chain teams simply do not have the bandwidth to take a manual approach. It’s not just the setup; recalculating landed cost is an ongoing task. Fortunately, other solutions are available:
Bring in experts
Engage external support, such as supply chain consultants or other supply chain experts, that have done this exercise many times and know all pitfalls when calculating landed cost for companies.
Add system modules
Purchase modules to already deployed systems such as Transportation Management Systems (TMS), Enterprise Resource Planning (ERP) systems, or supply chain design programs. The range of choice here is increasing as demand for accurate landed cost grows.
Deploy a Visibility Platform
The most advanced solution to achieve landed cost in real-time is to deploy a visibility platform that gives companies a single source of truth by connecting all parties and data in purchasing, shipping, storing and delivery. The heavy lifting to establish the cost data model and build live cost feeds needs to only be done once but will pay off in a very short time. For instance, without that visibility, companies could be losing money on a product they think is profitable.